Opening the Power of Welding WPS: Methods for Performance and Security in Construction
In the world of construction, Welding Procedure Specs (WPS) stand as the foundation of welding operations, dictating the required steps for achieving both performance and safety and security in the manufacture procedure. Recognizing the intricacies of WPS is extremely important to utilizing its full potential, yet many companies battle to unlock the real power that lies within these documents (welding WPS). By delving right into the methods that optimize welding WPS, a globe of enhanced performance and heightened safety and security waits for those going to explore the subtleties of this essential element of fabrication

Significance of Welding WPS
The significance of Welding Procedure Requirements (WPS) in the construction industry can not be overemphasized. WPS work as an important roadmap that lays out the needed actions to make certain welds are executed consistently and appropriately. By specifying vital parameters such as welding procedures, materials, joint layouts, preheat temperature levels, interpass temperatures, filler metals, and post-weld warm therapy needs, WPS provide a standard method to welding that enhances effectiveness, quality, and security in fabrication procedures.
Adherence to WPS helps in attaining uniformity in weld top quality, decreasing the chance of problems or architectural failures. This standardization likewise facilitates compliance with sector policies and codes, ensuring that produced frameworks meet the needed safety and security standards. Additionally, WPS documentation enables welders to replicate successful welding treatments, leading to constant outcomes across different projects.
Basically, the meticulous advancement and rigorous adherence to Welding Treatment Specifications are critical for promoting the integrity of welded structures, protecting against prospective dangers, and upholding the reputation of construction firms for providing high-grade services and products.
Trick Elements of Welding WPS

Enhancing Effectiveness With WPS
When maximizing welding procedures, leveraging the key elements described in Welding Procedure Specs (WPS) ends up being crucial for making best use of and simplifying procedures performance. One way to improve efficiency with WPS is by very carefully picking the appropriate welding parameters. By adhering to the details standards given in the WPS, welders can make certain that the welding tools is established up appropriately, causing top notch and constant welds. Furthermore, complying with the pre-approved welding sequences find out here now detailed in the WPS can considerably reduce the moment invested in each weld, eventually enhancing overall productivity.
Consistently assessing and upgrading the WPS to incorporate any kind of lessons learned or technological innovations can likewise add to effectiveness improvements in welding operations. By welcoming the guidelines established forth in the WPS and continuously seeking methods to maximize processes, fabricators can accomplish greater performance levels and exceptional end outcomes.
Ensuring Safety And Security in Construction
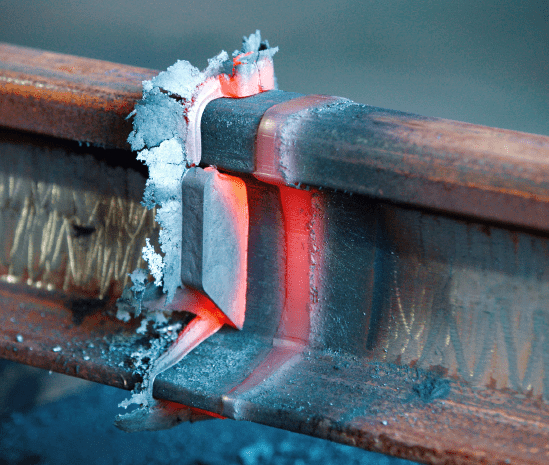
Guaranteeing safety and security in construction involves a complex method that incorporates different facets of the welding Clicking Here process. Welders have to be furnished with appropriate gear such as helmets, handwear covers, and safety clothes to minimize threats associated with welding activities.
In addition, adherence to correct air flow and fume extraction systems is critical in preserving a healthy and balanced workplace. Welding fumes include unsafe substances that, if breathed in, can pose severe health threats. Executing reliable ventilation procedures helps to lessen exposure to these harmful fumes, advertising breathing wellness among workers.
Normal tools upkeep and assessments are also necessary for ensuring security in construction. Faulty equipment can bring about injuries and mishaps, highlighting the relevance of routine checks and timely repair work. By prioritizing safety steps and promoting a society of recognition, fabrication facilities can create a effective and safe and secure job environment for their personnel.
Executing WPS Finest Practices
To improve functional effectiveness and make certain high quality end results in construction procedures, incorporating Welding Procedure Requirements (WPS) finest techniques is critical. original site Picking the appropriate welding process, filler product, and preheat temperature level specified in the WPS is critical for accomplishing the wanted weld quality. Making sure that certified welders with the required accreditations lug out the welding procedures according to the WPS guidelines is crucial for consistency and dependability.
Verdict
Finally, welding WPS plays a critical role in guaranteeing performance and safety and security in fabrication processes. By concentrating on vital elements, improving performance, and carrying out best methods, firms can maximize their welding operations. It is vital to prioritize security steps to prevent mishaps and guarantee a smooth manufacturing procedure. By adhering to these methods, organizations can unlock the full potential of welding WPS in their fabrication operations.
In the realm of construction, Welding Procedure Specifications (WPS) stand as the backbone of welding procedures, determining the essential actions for accomplishing both effectiveness and security in the fabrication procedure. By defining essential parameters such as welding processes, products, joint layouts, preheat temperature levels, interpass temperature levels, filler steels, and post-weld warm treatment requirements, WPS provide a standard technique to welding that improves effectiveness, quality, and safety and security in manufacture procedures.
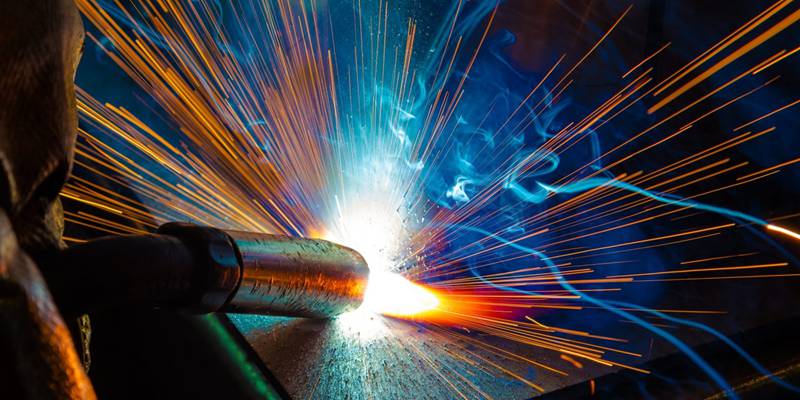
When enhancing welding operations, leveraging the essential components outlined in Welding Procedure Requirements (WPS) becomes vital for maximizing and improving procedures efficiency. (welding WPS)
Comments on “Welding WPS Explained: Key Components and Advantages for Your Welding Procedures”